サブマージアーク溶接とは?
サブマージアーク溶接(Submerged Arc Welding/略してSAW)は、造船や橋梁、圧力容器、厚板の建築構造物などで活躍する、超効率型の溶接方法です。
特徴は、粒状のフラックスを山盛りにして、その中でアークを発生させる点。つまり、アークも溶融池も、人の目には一切見えません。それでいて溶け込みは深く、厚板にも対応できるという…まさに“現場向けのプロ仕様溶接”。
実際に使われる現場
サブマージアーク溶接が使われるのは、次のような「大型かつ高精度が求められる分野」です。
造船(船体ブロックの突合せ溶接など)
橋梁(橋脚部や大型部材の接合)
圧力容器(ボイラー、熱交換器の胴体部)
建築鉄骨(大梁などの一発施工)
こういった現場では、1パスでどれだけ確実に仕上げられるかが求められます。
何度も溶接して手直し…なんて時間も余裕もない。サブマージはそんな状況で威力を発揮するんです。
サブマージのメリットとデメリット
◎メリット
特徴 | 内容 |
---|---|
高電流対応 | 1000A以上の高出力でもOK |
深い溶け込み | 板厚30mmでも1パスでOK |
自動化に強い | トーチの移動・ワイヤー送給・フラックス散布が自動 |
光を見ない | フラックスでアークを覆うから安全 |
ヒューム少なめ | 周囲環境にも優しい |
🔧 フラックスの役割
熱で溶けて溶融池を保護し、スラグとして不要物を包み込みながら外観も整える万能薬。
▲デメリット
特徴 | 内容 |
---|---|
開先のばらつきに弱い | トーチが自動で動くため、開先にムラがあるとビードが乱れる |
位置に制限がある | 粒状フラックスは下向き以外では使用困難(立向・上向き不可) |
状況確認ができない | アークも溶融池もフラックスに覆われて見えない |
設備費が高い | 溶接機器一式の導入コストが高く、中小では導入しづらい |
未経験者が現場で挑戦!?サブマージ体験レポ
さて、ここからは僕の体験談。
正直、サブマージアーク溶接なんて納品した仕事のクレームで、血相変えて現場へ駆けつける時にチラ見で横を通り過ぎるくらい。そんな僕がいきなり、
「オイ、やってみ」って言われたんです…
使用母材と条件
材質:SS400
板厚:22mm
形状:ロール加工された直径1.5mの筒材
条件:下向き突合せ溶接・1パス施工
「あれ?説明それだけ?」
冗談抜きで、説明はほんのわずか。
「これがこうで、こうな」ってだけで始めさせられました。
見えない中で、どうやって溶け込んでるのか?トーチの高さは?電圧の設定は?
そんな疑問が浮かぶ間もなくスタート。
これが脚長30mm!?でも結果は…
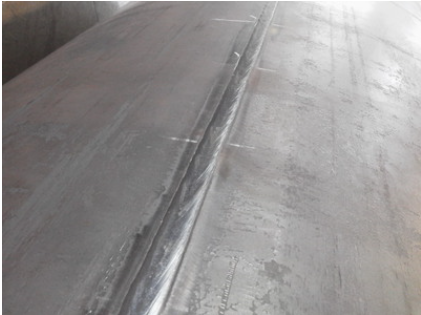
見た目の印象は…
ビードの波がかなり粗い
両端に軽いアンダーカット
一部に脚長不足
うーん。正直、大成功とは言いがたい。

職人との比較で凹む
このあと、無言で有名なベテラン職人の溶接も見せてもらいましたけどね、もう圧巻。
まるで鏡のように波ひとつないツルッツルなビード。
「これが同じ機械で出せるんか…?」と目を疑いました。
これは画像に残さねば! と思い聞いてみると、無言で突然の訪問販売業者を見つめる様な顔。
はーい、諦めます。
サブマージの“怖さ”と“優しさ”
今回、一番怖かったのは「失敗できない状況」だったこと。
練習用の破材なし(材料が高い)
成功前提のぶっつけ本番
溶け込みも様子も見えないまま進行
失敗したら材料も信用もパー
大先生が無言
「マジで怖いって!ほんとに!」
でも、そんな緊張感のあと、無言大先生が表情だけで「飯奢るわ。」の顔。
これはと思い付いていくと、昼飯ご馳走してくれました!
仕事離れると喋る喋る、いい人だった。
まとめ:自動化に頼れるのは、技術があってこそ
今回の体験を通してわかったのは、自動溶接=簡単ではないということ。
条件がズレれば結果も一気に崩れます。
そして、ベテランの設定技術や段取り力の差は、明らかにビードに出る。
「自動でも職人の腕が必要」
サブマージアーク溶接って、そういう世界なんだと実感した一日でした。貴重な経験をさせて頂きありがとうございました。